Decanter Connected Services
Alfa Laval Connected Services gives you the ability to collect data, self-monitor component condition, and cut service and troubleshooting times significantly for your decanter. It becomes easier to plan maintenance and service and avoid costly mechanical breakdowns, so your decanter spends more time creating value.
More uptime – less uncertainty
- Preventive or predictive approach to maintenance
- Optimizes protection of critical components.
- See performance and know how to quickly correct issues
- Consistently predictable and reliable standard of uptime
- Minimize disruption, enhance value
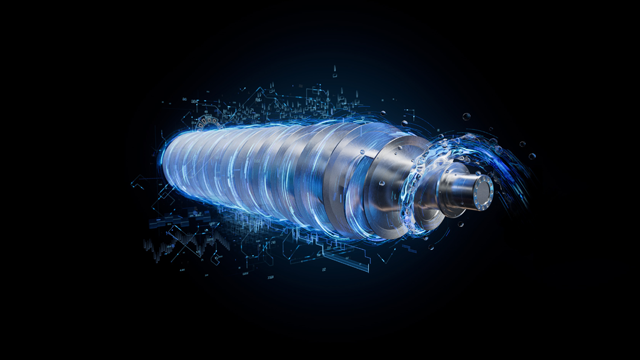
Experience optimal performance by connecting your decanter with these two essential services. Remote Support and Monitoring helps minimize lead times and expenses, ensuring maximum efficiency. And ConditionAlertTM works as a preventive maintenance solution to safeguard productivity, allowing you to proactively avoid breakdowns and maintain peace of mind.
Documents
Downloads
Remote Support and Monitoring
Shorten lead times and expense
- Monitor your decanter’s key running parameters in real time
- Data collected and stored on the Alfa Laval IoT (ALIOT) platform 24/7
- Alfa Laval Service experts use historical events to solve issues and guide you
- through service or trouble-shooting steps in a one-to-one session
- Troubleshooting and service instructions provided remotely, shortening lead
- times and saving expense of field service engineer
- Access alarms remotely from a mobile or tablet
- Assess if and what further steps are need without having to be onsite
ConditionAlertTM
More available, more productive
- Stop smaller breakdowns from become larger and more costly
- Foundation for full predictive maintenance, ensuring greater uptime and productivity
- Collects and assesses data 24/7, producing warnings and reports about changes in critical component status
- Convenient and cost-effective service scheduling
- More effective planning of spare parts and service team resources
- Data-driven insights help determine remaining lifecycle of key components
- Optimize operations to save resources and minimize spoilage of perishable
goods