Cut operating costs with Alfa Laval’s Connected Services for Wastewater Decanters including Condition Monitoring and more
Alfa Laval Connected Services add new possibilities to your Alfa Laval wastewater decanter such as remote support and monitoring, condition monitoring, predictive maintenance and process optimization. The results are lower service costs, maximum operating reliability, higher process efficiency and more uptime. Learn more about Alfa Laval’s Connected Services for decanters in wastewater plants in the sections below or contact us for a discussion on the best combination for your plant.
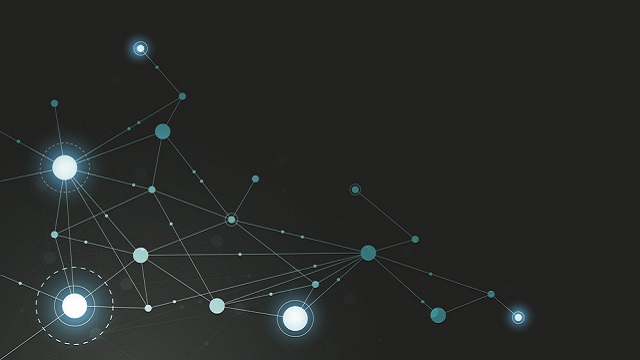
Remote Support and Monitoring
Faster, more accurate troubleshooting and quicker return to service.
Cost calculator
Lower operating costs and immediate feedback on the effect of changes.
ConditionAlert
Condition monitoring system enabling predictive maintenance and optimum service intervals.
Constant Solids Load and Adaptive Polymer Control
Optimized process and polymer consumption.
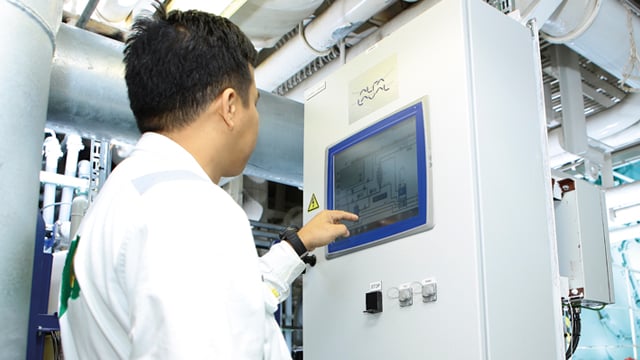
Bringing the benefits of IoT to the wastewater industry
Over the last 30 years, the Internet has revolutionized the way humans interact. The next step in the evolution of digital communication is the interconnection of machines, sensors and various digital systems. This is commonly referred to as the Internet of Things (IoT) and brings completely new possibilities to increase efficiency and add value to customers.
Alfa Laval is taking an active part in this development. With our IoT services for wastewater plants, our customers get new possibilities to cut service and polymer costs, increase reliability and increase overall efficiency. We are investing heavily in R&D and we will continue to release new IoT services as technology progresses.
Remote Support and Monitoring
Alfa Laval Remote Support and Monitoring gives you the fastest and best support from Alfa Laval. Our service experts will provide you with valuable advice on maintenance, service planning, process optimization and troubleshooting. Your wastewater decanter centrifuge is connected to Alfa Laval’s monitoring system via internet, allowing our staff to access its data remotely and support you in the best way.
Fast and accurate help
With Remote Support and Monitoring, our service engineers can monitor your decanter centrifuges' operating parameters remotely when you call them for support. This minimizes time for diagnosing problems and sending spare parts in case your decanter needs servicing or repairing.
Remote access
Remote Support and Monitoring also gives you remote access to your decanter centrifuges through Alfa Laval’s service web. Technical data can be analysed through a web interface, making it easy to benchmark different decanters and optimize operation. There is also an option to send alarms via SMS or email.
Benefits
- Support by Alfa Laval experts
- Faster and more accurate troubleshooting
- Faster return to service in case of problems
- Access your equipment remotely to see operating data
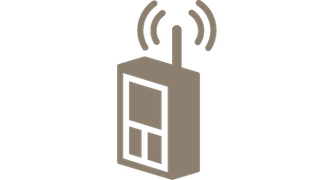
Cost Calculator
The Cost Calculator is an add-on to Remote Support & Monitoring that helps optimize operating cost. The Cost Calculator algorithms make a real-time calculation of your operating cost based on live operating data and factors such as the price for polymer and power. The Cost Calculator clarifies the impact that different actions have on operating cost and increases awareness among the staff.
Benefits
- Lower operating costs thanks to increased cost awareness
- Immediate information on how different settings on your decanter affect cost
- Identify and share best practices between sites and different decanters
- Facilitates forecasting of polymer consumption
ConditionAlertTM
ConditionAlertTM is a condition monitoring system for your Alfa Laval decanter centrifuge that allows you to make predictive maintenance and optimize service intervals. In most cases this reduces service costs and increases operating reliability.
A set of sensors keeps track of the condition of critical decanter’s components. The data is sent to a central server for analysis and if any anomalies are detected, the system alerts Alfa Laval’s service engineers who assess the situation and contacts you for planning of service well before any problems arise.
Benefits
- Optimized service intervals, most often leading to longer intervals and lower service costs
- Maximum operating reliability
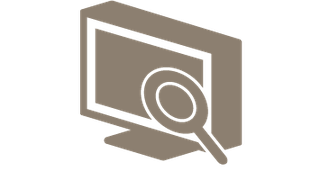
Constant Solids Load and Adaptive Polymer Control
This is a process optimization system that helps wastewater plants reduce operating cost for their Alfa Laval decanter centrifuges by optimizing the dosing of flocculants. There are two ways you can set this system up, either in Constant Load mode or in Adaptive Polymer Control mode.
Constant Load
When optimizing the process for constant load, the system keeps the amount of solids passing through the decanter constant. This is done by measuring the concentration of solids in the feed and continuously adjusting the flow rate to keep the solids load constant.
Stabilising the solids load for the decanter this way makes it easier to optimize its operation, e.g. dosing of flocculants, thus reducing operating costs.
Adaptive Polymer
The other option for process optimization is to keep the feed flow constant whilst continuously adjusting the amount of flocculants being added. In this case the system measures the solids' concentration in the feed and adjusts the dosing of the flocculants accordingly. This optimizes the consumption of flocculants and cuts operating costs.
Benefits
- Optimized process and polymer consumption
- Reduced operating costs
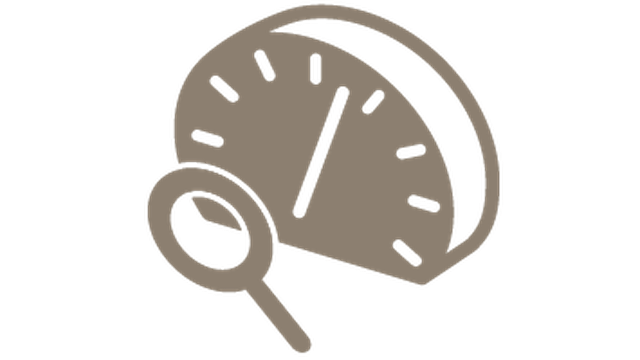
Part of a Service Agreement
We offer our Connected Services as part of a Service Agreement. These tailored service packages can include service from our broad range and come with a fixed annual fee. Based on your priorities and conditions we help you find the ideal service solution.
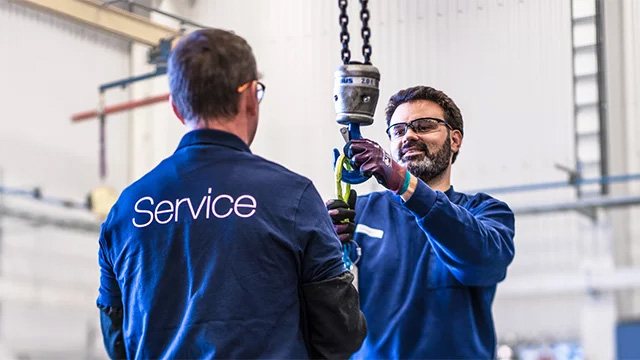