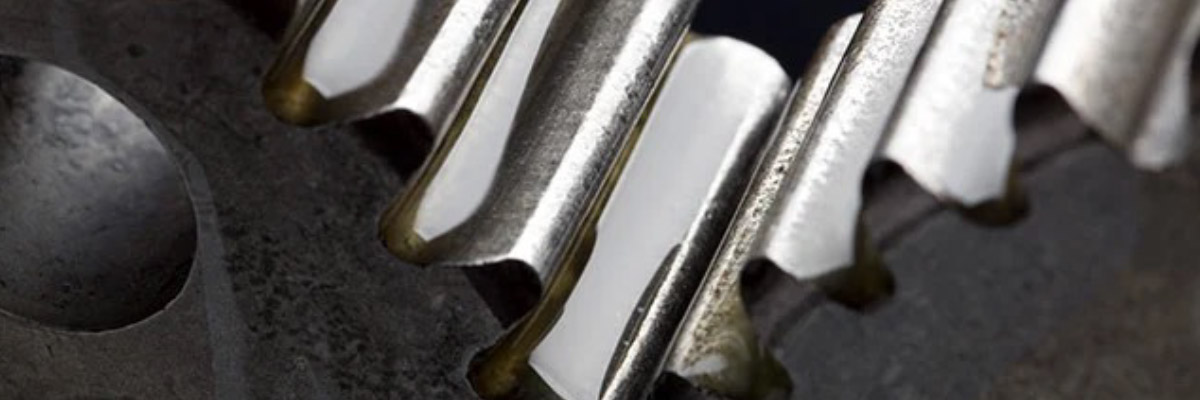
Integrating cat fine defence
Cat fines remain a major threat to marine engines, appearing in even higher concentrations since the move to low-sulphur fuel oils. At the same time, new variables have entered the fuel mix, such as blends of low-sulphur fuel oils with biofuels. To protect marine engines, shipowners and operators must handle the increased complexity, which requires more than just advanced equipment. It takes solid knowledge of fuel management, fuel line design and operational best practices.
Seeing the fuel line as a whole
When working with oils as fuel, removing contaminants before the fuel reaches the engine is one of the fuel line’s primary tasks. Although most of that burden falls on the separators, maximizing protection depends on multiple components:
- Settling tanks
After bunkering, enough oil is pumped from the storage tank into the settling tank(s) to support 24–48 hours of operation. As the name implies, some larger cat fines and an amount of water will settle out there with the help of gravity. But settling isn’t nearly enough to protect the engine, and rough seas can send settled contaminants further into the fuel line. - Separators
Separators (also known as purifiers) are the primary defence against cat fines. Using centrifugal force, they remove not only cat fines but also water and other contaminants – such as asphaltenic sludge – before the fuel enters the service or day tank. Fuel density, viscosity, temperature and feed flow rate are all critical factors for separator performance. However, today’s fuel characteristics are less homogenous than ever, especially when biofuels are blended in. - Fuel supply systems
Fuel supply systems (also known as boosters or fuel conditioning systems) perform the final processing of the fuel before it enters the engine. Given today’s more complex fuel characteristics, they need sophisticated automation to ensure the correct fuel temperature, viscosity and pressure for injection. In addition, they provide a fine filtration step – a crucial last line of cat fine defence. - Flow control systems
Automatic flow control is an underutilized tool that improves both cat fine removal and energy efficiency. Since slow steaming is the norm on most vessels today, few separators need to run at 100% capacity. Flow control systems like Alfa Laval FlowSync continuously synchronize the separator feed flow with the engine’s actual fuel consumption, which optimizes separation performance and minimizes energy usage.

Making an informed choice of separators
Since separators are the main defence against cat fines, their sizing and performance are crucial. Separators can be run individually or in parallel. But to remove cat fines effectively, they must have sufficient cleaning capacity for the intended flow. Having their performance measured and validated by a third party makes it easier to compare separators from different makers.
Certified Flow Rate (CFR) for separators was introduced through a workshop agreement in 2005. CFR testing uses spherical particles of 5 microns in size, which are mixed into oil to simulate cat fines. The CFR on a separator’s certificate is the rate at which 85% of the particles are removed at normal treatment viscosity.
The original workshop agreement, CWA15375:2005, expired in 2014. But the testing procedure has remained in use due to the valuable transparency it creates. In 2022, an improved standard was finally released: EN 17763:2022. Unlike the original agreement, which allowed individual test results to be scaled across multiple separator sizes, today’s CFR standard requires testing of each size within a separator range.

Creating an integrated fuel line system
Although separator sizing is critical, there’s much more to fuel line success in today’s fuel landscape. Apart from unpredictable cat fine levels, variations in fuel viscosity, lubricity and temperature have profound implications for safe and reliable operation. Maximizing engine protection depends not only on multiple components but also on interactions throughout the fuel line.
It's therefore important to avoid commodity thinking. Separators should be viewed as part of the wider system, complemented by properly configured settling tanks, sophisticated fuel conditioning and automatic flow control. The entire fuel line should be considered as whole, with each component contributing to the overall objectives.
Above all, shipowners and vessel designers should take the lead in decisions related to engine protection. Specifying the entire fuel line is far better than leaving individual choices to the shipyard.

Human expertise is equally important
No matter how well the fuel line is designed, knowledgeable crews are also needed to keep the engine from harm. Today’s diverse fuel scenarios demand deeper understanding and even greater vigilance:
- Testing and monitoring
Operators must be aware of potential fuel dangers, which include today’s significantly higher cat fine levels but also stability, incompatibility and degradation risks – especially where biofuels are concerned. Lab testing is the gold standard, but crews should also test and monitor on board whenever possible. The better they understand the bunkered fuel, the lower the risk of incidents will be. - Detecting signs of damage
Apart from spotting problems with the fuel itself, crews must be alert to early warning signs of equipment damage. Lower pressure, sump contamination and drops in engine efficiency can all be indicators that serious damage is occurring. By responding immediately, operators can mitigate both further damage and costs. - Maintenance and service
Proper operation of fuel line equipment depends on good housekeeping and proper care. Periodic cleaning of tanks, for example, will ensure that settled cat fines are not reintroduced into the fuel flow. Likewise, crews must perform the regular equipment inspections and maintenance required. While the selected equipment should be easy to service, knowledge is still needed – along with global access to skilled service technicians when issues exceed crew expertise.
All this makes effective training programmes more vital than ever. As the International Chamber of Shipping pointed out in a 2021 study, the industry faces a shortage of skilled crews worldwide. Fleet technical programmes to manage engines and equipment need to be supported by actual knowledge among those on board.
Simply put, a holistic, integrated approach to the fuel line and cat fine protection includes the crew as well as the equipment.