Pyrolysis
To accelerate the net zero transition, we need technologies that enable and complement conventional recycling methods like mechanical recycling (PET).
Pyrolysis is the dominant recycling technology for the future. Recycling via pyrolysis converts low-value waste, such as plastic, tires and biowaste, into new materials.
Alfa Laval know how enables you to reach:
- Energy efficiency and fouling corrosion abatement
- High yield quality and plant operation uptime
- Efficient water and waste management
Optimizing the upgrading process of your pyrolysis product
By 2050, over 50% of the carbon in chemicals is projected to come from recycled sources. Pyrolysis is identified as a promising technology for converting waste into valuable pyrolysis oil (pyoil). However, pyrolysis processing faces challenges such as high viscosity, water content, low heating value, and stability issues. Effective separation and filtration technologies, particularly centrifugal separation, are crucial for improving pyoil quality and yield.
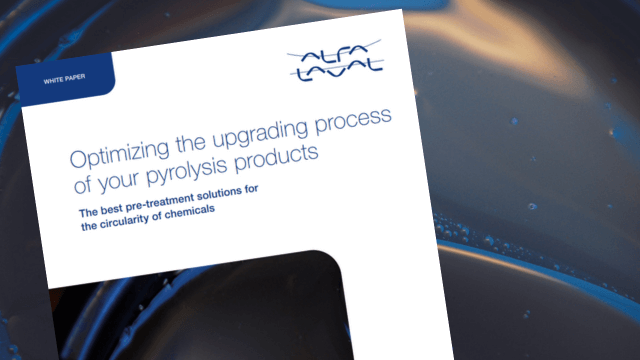
Unique challenges of pyrolysis
The pyrolysis process is particularly effective for waste plastics that may otherwise be difficult or impossible to recycle. By converting these plastics into valuable chemicals, it provides a viable solution for their reuse or disposal. Ultimately, pyrolysis lets us reduce the negative impact of plastic waste on our environment, while creating profitable opportunities for businesses. Although it has a promising future, pyrolysis is not without challenges, particularly with regards to the technology. The challenges are diverse and varied, with each one presenting unique difficulty:
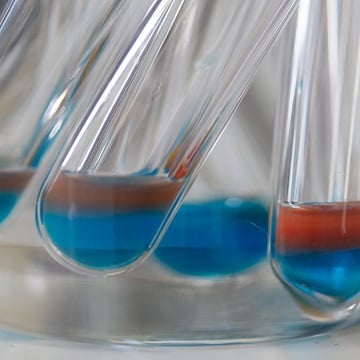
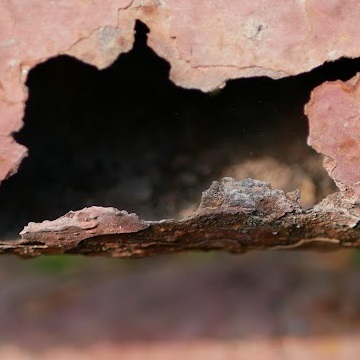
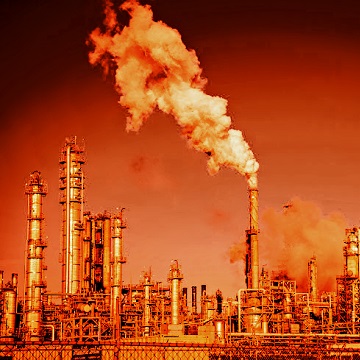
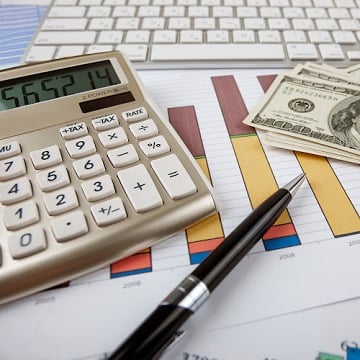
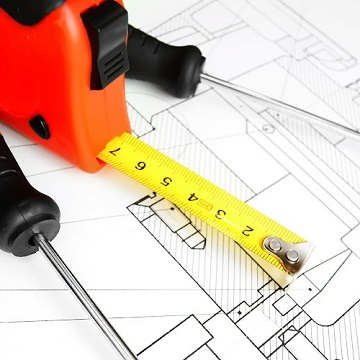
Challenging fluids
Varied batches: viscous, long-chain hydrocarbon-filled feeds
Corrosion & fouling
High-prices, specialized equipment needed for harsh conditions.
Emissions
Energy-intensive process, high heat and costly by-product disposal.
Economics
Costly energy and installation affect ROI and margins.
Scalabillity
Tight timelines, limited space and flexible hinder quick launches.
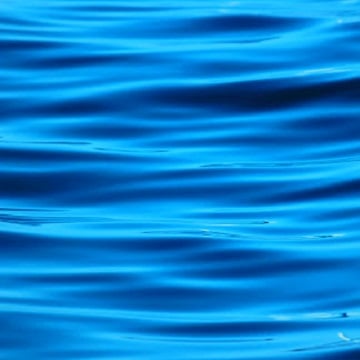
Water management
Products require cooling, cleaning and separation, that all lead to water pollution.
Alfa Laval offering
Alfa Laval’s core technologies, such as disc stack separators and heat exchangers, optimize the production and upgrading of pyrolysis products. That means decontaminating and treating the pyrolysis oil, preventing fouling of viscous fluids and utilizing waste heat in a smart way.
In addition, the contaminated water is cleaned, and the waste is minimized, complying with environmental regulations and targets to reach net zero.
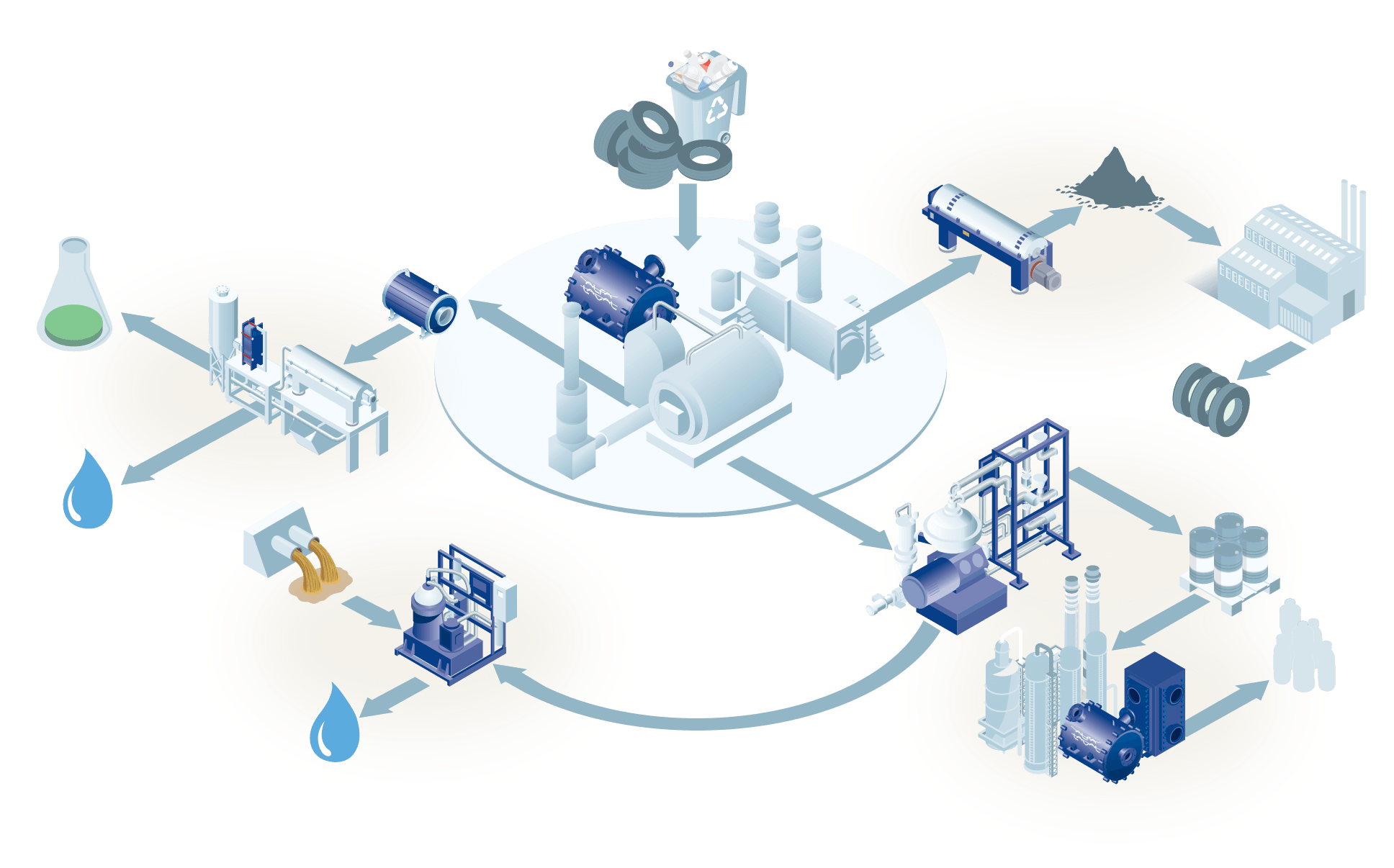
Disc stack separators
Our separators enhance the purity of pyrolysis oil significantly. The centrifugal forces strike out and efficiently remove contaminants, such as water, ash, and tar. This way the oil can be further processed into valuable polymer to produce renewable chemicals and recover the solids into carbon mass.
Spiral heat exchangers
This innovative technology provides superior adaptability to changing feeds and heavy fouling fluids. It improves the reliability of processing pyrolysis oils. All packed together in a solution that is easy to open and easy to clean.